Tuesday, August 30, 2022
PTFE Products - Teflon PTFE Hose Pipe Tube
Monday, August 29, 2022
PTFE Plays A Vital Role In The Turn Of Cable-stayed Bridge
China’s first sea-crossing high-speed railway between Fuzhou and Xiamen is coming, on which the cable-stayed bridge has been built successfully with the help of PTFE polytetrafluoroethylene, the king of plastics. Let’s talk about an application of PTFE that is little known to you.
Taicheng Xite Bridge is one of the bridges between Fujian and Xiamen High-speed Railway. The bridge is designed as an unbalanced rotating cable-stayed bridge with a total weight of 38,000 tons. The total length of the rotating part is 221.3 meters, which is the largest unbalanced rotating cable-stayed bridge of high speed railway in China in terms of tonnage.
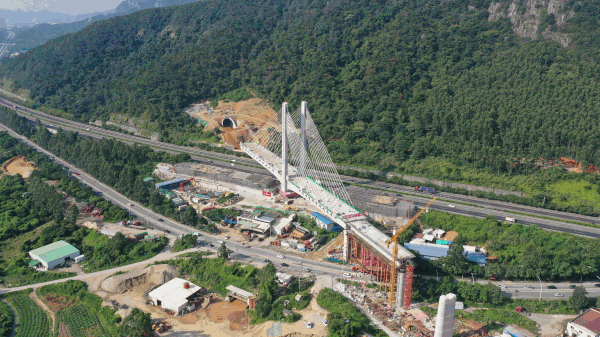
How does such a huge object with such a tonnage complete a “gorgeous transformation”? This can’t be done without a high-performance fluoropolymer: teflon sliders. How can a small Teflon slide make a 10,000-ton bridge turn freely?
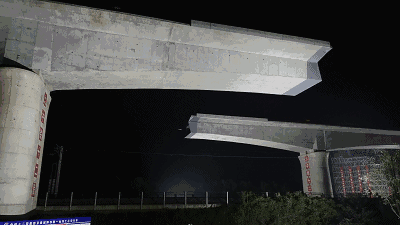
The basic principle of the rotating body is to set the ball hinge sliding layer between the upper and lower structure of the rotating body which is resistant to high pressure and has a small coefficient of friction. The ball hinge is composed of upper ball hinge, modified teflon slider and lower ball hinge, with the upper and lower ball hinges located in the upper and lower turntable.
In simple terms, the principle is similar to that of a stone grinding disc, where the base does not move and the upper part rotates around the grinding center. So the friction force between the ball hinges needs to be overcome during the traction rotation. How to reduce the frictional resistance is the key technical problem in the construction of the rotating body.
PTFE slider plays such a vital role due to its excellent self-lubrication, lowest dynamic and static friction coefficient, and wear and pressure resistance. After completing the installation of PTFE slider, the upper and lower ball hinges and the central shaft are coated with teflon powder grease lubrication medium, which can minimize the friction. In addition, the rotating shaft has PTFE tube, which can reduce the friction generated in the process of turning the body. Such a small PTFE slider should have such amazing energy!
Features of PTFE
● High temperature resistance
Its working temperature can reach up to 250 ℃.
● Low temperature resistance
It has good mechanical toughness at low temperature; even if the temperature drops to -196 ℃, it can keep 5% elongation.
● Corrosion resistance
It’s inert to most chemicals and solvents, and can resist strong acids and alkalis, water and various organic solvents.
● Good weather resistance
It has the best aging life among plastics.
● High lubrication
PTFE has the lowest coefficient of friction among solid materials.
● Non-adhesive
It has the lowest surface tension among solid materials, and does not adhere to any substance.
Applications of the king of plastics
PTFE can be made into sheets, tubes, rods, films, fibers and coatings according to product classification, and is widely used in various fields such as chemical, petroleum, textile, electrical and electronic, medical, mechanical and aerospace.
● Medical
PTFE is water resistant, physiologically inert, and non-adhesive, so it is used in many tissue repair materials and artificial organ materials, such as artificial blood vessels, and heart repair membranes, etc. PTFE can be sterilized using any method, and will not degrade when heated under high pressure or treated with various disinfectants. Therefore, it is widely used in medical devices such as sutures, sterile pads, and injection needles.
● Electronic and electrical
PTFE has excellent dielectric properties and extremely high thermal stability, and is an irreplaceable electrical insulation material, playing an important role in the field of electrical and electronic insulation. For example, PTFE glass lacquer cloth is used to produce high temperature and high frequency insulation materials, which can be used in satellite communications and computers; PTFE film is used to make capacitors as an insulation layer, padding and cables between instruments; PTFE thin-walled tubes of different calibers can be used for lead wire sleeves, heat shrinkage tubes and spiral tubes, and insulated lead pipes for generators, etc.
In the field of 5G communications, PTFE is also widely used in base station filters, high-frequency high-speed PCB/FPC, 5G chip process and high-frequency connectors and cables. Currently, the 5G filters used by major communication equipment vendors are still made of metal cavity filters, which use many PTFE components for support and insulation.
● Mechanical
For any kind of machine and equipment, lubrication should be conducted for mutual sliding surface during the operation to reduce the friction factor, reduce the wear and heat of the parts, ensure the normal operation capacity, accuracy and power consumption of machine and equipment. PTFE’s low coefficient of friction and self-lubricating properties allow it to be used in the manufacture of bearings, piston rings, machine tool guides and sealing materials, but it is usually used in precision instruments or acid and alkali resistant environments because it’s expensive.
● Textile
Expanded PTFE (e-PTFE) film is laminated with common fabrics to make waterproof and moisture permeable laminated fabrics. Its excellent characteristics of high strength, low shrinkage, non-stick and anti-UV aging enable e-PTFE fiber to become the fabric of choice for outdoor sports clothing. In addition, it is often made into firefighting suits, astronaut suits, medical protective suits, military combat suits, sleeping bags and lightweight tents.
● Automotive & transport
In the automotive oil seal material, it can isolate the parts that need lubrication in the transmission parts from the outgoing parts to prevent the leakage of lubricating oil. PTFE breathable film is used in automotive lights to balance the pressure inside and outside the lights and prevent the pollution brought by water, dust, and automotive fluids, etc.
● Chemical
PTFE, by virtue of its corrosion resistance, is used as an anti-corrosion material to make various anti-corrosion parts, such as pipes, valves, pumps and pipe fittings. For chemical equipment, it can make lining and coating for reactors, distillation towers and anti-corrosion equipment.
Find the best PTFE manufacturer
To make the most use of PTFE products, you’d better choose the best PTFE manufacturer and SuKo, a China well-known PTFE tube manufacturer, is you best choice. Expert in PTFE/UHMWPE extrusion and products in various types and models, Suko stays forefront of the Tetrafluorohydrazine industry with technology innovation,profession and intelligence both domestically and abroad.
Basics Of Multi-lumen Medical Tubing
Multi-lumen tubing extrusion technology
The breakthrough in multi lumen medical tubing extrusion technology has promoted the application of medical tubes to a new level.
In the medical device industry, the minimally invasive surgery rends to require smaller and more innovative medical devices. Devices that act on blood vessels or other tissues require medical tubes with higher precision, tighter tolerances and additional functions. As the tubes are designed more complex, the extrusion technologies to produce them become more complicated. There is no doubt that the multi-lumen tubing extrusion technology is at the forefront of extrusion technology.
Multi-lumen extrusion or co-extrusion can be defined as the simultaneous extrusion of multiple layers of materials to produce multi-lumen medical tubes. Multi-lumen technology is primarily used to improve functionality: combining weldable materials with materials that have certain other performance characteristics, such as lubricity. These structures can also improve performance and potentially reduce overall assembly and material costs, making medical devices more cost-effective for customers; other features may include the addition of active material layers, such as hydrophilic, bioabsorbable or drug-eluting layers. The technologies and materials available to produce multilayer products for medical devices have greatly improved and offer designers a wide range of options for optimized size, material and function.
The functions of medical PTFE multi-lumen tubing in medical devices include: creating tubing surfaces with different characteristics for external and internal surfaces; combining materials with different characteristics to create unique tubing characteristics; enabling active materials to be optimally located; locating bondable materials internally or externally for self-assembly and easy assembly of complex medical devices.
The processing of multi-lumen tubes requires technicians to piece together a wide variety of extruders and downstream equipment. With this poor approach, it is likely that the various extruders will all be in the same plane, resulting in longer flow paths, increased extrusion pressure and increased material processing time. Under such processing method, the required tube layer ratios do not match the optimum output of the extruder, which can result in too high or low screw speeds, and further produce tubes with poor mechanical properties.
Modern multi-lumen tubing extrusion processing equipment is more likely to be a fully integrated production line with a single operator interface that monitors, controls and records the entire extrusion system in real time. Extruders for each polymer layer are selected to provide the desired range of output speeds that do not compromise the mechanical properties of the material. They are positioned to minimize material residence time, and typically one or more extruders can be mounted vertically or at a 45° angle. Typically, one or more extruders in a multi-lumen system will be micro-extruders with a minimum output of 50 grams per hour, allowing an individual layer to be just a few microns thick. Manufacturers of these micro-extruders use innovative extruder designs to ensure that standard plastic pellets travel well through the feed section of the extruder without loss of stability.
Customer expectations are driving the massive use of such statistical process control system and increasing product requirements from regulatory agencies. However, accurate in-line measurement of thin wall medical tubing remains a considerable challenge for medical device manufacturers.
There are still quite a few thermoplastic materials that can be used to design multi-lumen tubes. The most commonly used materials are those traditionally used to make medical tubing, such as polyamide (PA), thermoplastic elastomer (TPE), polyurethane (PU), polyvinyl chloride (PVC), and polyolefin (PE). These materials can be customized to include drug-eluting components, radioactive materials, fillers, and/or colors. However, the designer must consider the processing temperature, flow characteristics and melt viscosity of the material.
Multi-lumen tubing extrusion technology is particularly suitable for extruding novel or active expensive materials that have specific functions because it allows for proper design of the placement of these materials on the medical tubing. A common example is: placing drug-eluting materials on the outer layer of the tubing or placing highly lubricated materials on the inner layer of the tubing. Furthermore, multi lumen medical tubing has cost advantages because thin layers can be placed in the most effective locations.
Applications of multi-lumen tubing in medical industry
Percutaneous replacement of a diseased heart valve is an emerging therapy that offers an alternative to traditional surgical approaches for high-risk patients. In this minimally invasive procedure, a guide wire is passed through the femoral entry site and guided into the heart chambers. A guide sheath is inserted over the guide wire, and the valve delivery system is introduced. The medical tubing required to deliver the valve to the site is a highly specialized component. The distal end must be easily manipulated so that it can be guided directly into the cardiac chamber. The proximal end needs to be more rigid, must have excellent kink resistance, and the inner diameter needs to be lubricated for smooth and unobstructed delivery of replaced valves. Another key requirement is that the wall should be as thin as possible to maximize the delivery path diameter of the replaced valve without the tube losing any of its function.
Designers faced many challenges in designing this particular component. PTFE lubricated liners usually meet the industry standard for delivery systems, but cannot be used due to the possible effects of gamma radiation during sterilization. To ensure that the medical tubing does not kink or deform as it is guided through the anatomy to the heart, a braided layer must be incorporated into the component.
The final design is a five-layer assembly consisting of an ultra-thin-walled multi lumen medical tubing, a braided layer of stainless steel and polyether block amide sheaths of various hardnesses, adding overall proximal to distal flexibility to the outer layer of the assembly.
Conclusion
The innovative use of multi-lumen tubing in medical design has revolutionized the way we solve a large number of medical problems. In the future, as extrusion tools and machine design techniques become more advanced, coupled with improvements in process control and measurement systems, SuKo, one of China top 10 medical tubing companies expect to achieve greater precision with smaller, thinner and more versatile multi-lumen tubes. Over time, multi-lumen extrusion production lines will become more specialized and other extrusion technologies are incorporated such as multi-lumen extrusion, tapered extrusion, and intermittent/interrupted extrusion.
Wednesday, August 17, 2022
Polyteflon Resin Poly Tetra Fluoro Ethylene PTFE Teflon Virgin Molding Powder
Tuesday, August 16, 2022
PTFE Products - Stainless steel braided Teflon liner Tube pipe - The production process
Monday, August 15, 2022
PTFE Products - PTFE Teflon Film by SuKo
Thursday, August 11, 2022
CNC Rotary Cutting Skiving Machine for UHMWPE PTFE Teflon Film
Wednesday, August 10, 2022
PTFE Products - Teflon Super Huge Large Size Tube Rod Plate Pipe
Wednesday, August 3, 2022
PTFE Products - PTFE Teflon Tube Pipe by SuKo
How do medical multi-lumen tubing help the fight against Covid-19
Amid the Covid-19 virus outbreak, medical PTFE multi-lumen tubing is playing an important part in helping fight the global pandemic. In this article, SuKo will explain what medical tubes are, how they’re used and why they’re helping in the fight against Covid-19.
What are medical tubes?
Medical tubes are used as part of equipment to deliver fluids to and from the body, and can also be used for catheters and respiratory equipment. Some medical tubing should be custom produced with different chambers or cores for delivering medication to the body. Medical tubing has become an essential component in the fight against Covid-19 considering the increased number of ICU patients and the increasing demands for ventilators and other respiratory equipment.
What plastic is used for a medical tube?
PTFE is one of the most commonly selected plastics for medical tubing, because it’s adaptable and can be sterilized. Other types of plastic used in medical grade tubing include more flexible materials such as PVC, TPU, TPE, and TPV, etc.
Sterilization and antibacterial properties of medical tubes
Although single-use plastic is frowned upon in everyday life, it can help prevent the spread of viruses and diseases in the medical profession, which is because it’s more hygienic to dispose of items used to treat those with highly contagious viruses rather than to re-use products.
According to medical tubing companies, medical grade plastics should be able to withstand high temperatures and corrosion for optimum cleaning in places where medical equipment is safe to be sterilized and cleaned. Some medical grade plastics can be fitted with anti-bacterial protection to help prevent the spread of contagious illnesses in hospitals and healthcare environments.
How are medical multi-lumen tubes helping the fight against Covid-19?
Medical multi-lumen tubes, key component of medical devices and respiratory equipment including ventilators which aid breathing, have been used in healthcare for many years to enhance patient care and are critical to patient care in intensive care units. As you know, one of the known symptoms of Covid-19 is shortness of breath, which results from the fact that the virus attacks the lungs and pneumonia and respiratory complications will also occur to people with severe symptoms. Therefore, thin wall medical tubing is helping keep patients affected by the disease alive.
Find out more about medical tubing here . If you have an urgent enquiry about medical grade tubing you can contact our team on info@sukoptfe.com.